汽院因“东风”而生,依“东风”成长,服务“东风”和民族汽车工业不仅是汽院人应尽的责任,也是我们赖以发展壮大的基础。学校已走过50个年头,我也在汽院工作、生活了40余载。期间,我和同事们与东风汽车公司各专业厂密切接触,坚持走产学研合作之路,合作开展技术研发和人才培养,想以此谈些感悟。
一、起步艰辛初战告捷
那是1989年8月初的一天上午,机械原理与零件教研室副主任田福秀老师找到我说,二汽锻造厂热处理车间的生产线,使用的是五十年代老设备,汽车前梁和半轴的淬火、回火炉之间采用抛料淬火,操作工人把炙热的工件搬上回火炉的进给链。前梁重达50多公斤,工人一天要搬送几百次,劳动强度大,作业环境恶劣,不利于身体健康;拋料淬火导致产品硬度不均匀,达不到技术要求,返修率高,造成人力、物力的浪费;生产过程油液飞溅,经常发生着火事故,不安全而且污染环境。锻造厂领导希望我们学校帮助解决上下料的老大难问题。田老师想接下这个课题,问我能不能负责课题的机械设计。我虽然在武汉理工大学做过一些机械设计项目,仅是项目参与,当时心里没有把握,但我说可以试一试。在田老师的策划和组织下,《汽车前梁及半轴自动淬火机械手传动装置》科硏项目组很快正式成立,具体分工是,我负责机械设计,黄金喜、陈焕来老师负责电气设计,田福秀为项目总负责人,并于8月底与二汽锻造厂签订了研制“机械手”的项目合同。
没有一张图纸可借鉴,没有一台样机可参考,怎么办?困难并没有吓倒我们。我们利用校企联合搞科研的优势,和二汽锻造厂等相关人员多次讨论,反复修改和论证总设计方案。功夫不负有心人,终于在1990年4月完成了全部设计工作。
“机械手”样机的试制在二汽专用设备制造厂进行。样机安装后要进行预调试,前梁工件徒手上料到下料需要7-8人,课题组人员齐上阵,人手不够,还请了几个工人,为实现早日投入生产,我们加班加点,夜以继日。有一次从二汽专用设备制造厂回学校的路上,沈际春老师骑自行车带着我不慎摔倒,头部鬓角刺伤了一道裂口,立即送到二汽红卫医院缝针包扎。由于调试时间紧迫,我第二天忍着伤痛毅然参加了预调试。经过全组人员坚持不懈地努力以及厂校密切配合,1991年2月3日,具有九十年代先进水平的自动淬火装置“机械手”样机终于诞生了。样机研制成功,全组人员由衷地喜悅,所有的疲劳丢到了脑后。图1为全组人员在二汽专用设备制造厂进行样机预调试的合影。

图1 项目组人员样机预调试现场合影
我们在兴奋之余也有缕缕忧愁,“新生儿”能不能上生产线?上线后是成功还是失败?心中没底。我们请来了二汽锻造厂的有关人员进行了设备预验收。在验收过程中,厂方总师吴亨松、丁芝林等组织技术人员结合生产实际,认真研究,反复论证,最后确认该“机械手”可以上生产线。厂方同意上生产线,只是成功的开始。大家都明白,二汽是现代化大规模生产,前梁、半轴淬火任务完成的如何,直接影响到二汽的产品产量。“机械手”能否正常运行,能否达到设计要求和技术性能指标,还要靠实践来检验。课题组人员更加清楚,这是最后的冲刺,劲儿只可鼓不可泄,只能迎难而上,变压力为动力,只许成功,不许失败。
厂方根据生产需要只给了20多天的安装调试时间,炉子要改造,地基要挖深,“机械手”要安装调试,工艺流程也要发生较大的变化,时间紧,任务重,人员少,压力大。全组人员象开足了马力的机器,日夜不停轮流值班,二十四小时不合眼是常有的事。锻造厂上下齐动员,在人力、物力上给予大力支持和密切配合。在厂校双方的共同努力下,经过一个半月的安装调试及试生产,该设备达到预期的各项设计要求和技术性能指标。5月15日,厂校双方代表在竣工单上履行了签字手续,“机械手”正式投入生产。
“机械手”从设计到投入使用,共用了一年零九个月。在这段时间里,全组人员付出了辛勤的汗水,花费了大量的心血,多少个节假日没休息,多少个昼夜加班,谁也说不清楚。1989年底,田福秀老师已到退休年龄,但她为了民族汽车工业的腾飞,为了“机械手”的研制成功,依然勇挑重担,担任课题负责人。作为“机械手”的总设计师,除了绘图、描图、制造、安装、调试工作外,她还要做好厂校双方的协调工作;在课题攻关的关键时刻,黄金喜老师家里发生不幸,但她忍着巨大的悲痛坚持课题研究,在电器设计和控制柜安装上花费了大量心血;陈焕来老师,是一位实践经验丰富的老师,在安装调试中,他的手被机器碰伤缝了数针,线未拆就到了现场;实验室沈际春老师听说设备预调试需要增加帮手,二话没说加入到设备调试行列之中;学校时任机械工程系主任的李彦璐老师也给予了大力支持。
我现在还清楚地记得,当时在第一实验楼绘制图纸时正是冬天,没有暖气,没有电热炉,晚上干到凌晨手都冻麻木了。就在这样的环境中,大家坚持绘制出了数百张图纸。安装调试期间,同志们吃住在厂里,边摸索、边试验、边改进,分析故障产生的原图,及时排除故障。有一天现场调试,电阻带加热炉内的输送装置坏了,需要进炉内焊接。我进去帮忙扶工件,眼睛被电弧光刺伤,住在亲戚家,到了晚上眼睛红肿得厉害,什么也看不见,走路都需要搀扶,最后亲戚找来了母乳点滴才见好转。第二天,我仍然坚持到车间调试。工人师傅们说:“常老师最辛苦,活比我们干得都多,工作服比我们的还脏。”
“汽车前梁及半轴自动淬火机械手传动装置”项目投入生产运行后,使用情况良好,被二汽授予“技术进步质量效益杯一等功”。“机械手”的研制成功,填补了我国汽车工业大尺寸零件自动淬火装置的空白,属国内首创。尽管起步艰辛,但初战告捷,成功迈出了校企合作共同开发新装备(产品)的第一步。
二、解决急需,再克难关
东风散热器有限公司原来生产散热片的专用冲压机床,是二十世纪七十年代的设备,因长期高负荷运转,有很多传动零部件严重磨损,致使其运转不平稳、振动冲击大、噪音高,零件加工精度急剧下降。尽管经过多次维修,该设备仍不能满足产品的质量要求。公司决定将该设备报废,并派人多次到市场和有关厂家调研并准备购置,但市场上根本买不到所需设备。为满足生产的需要,该公司决定将已经闲置的可用设备J23-40型开式可倾压力机进行改造,并要求满足自动送料的需要,于2001年3月确立为“多品种散热片冲压自动线改造”项目。该公司主要生产散热器,但设计改造散热器装备的技术人员力量不足。正当公司为组建项目设计组着急之时,公司毕业在该公司技术科工作的技术员黄爽亮给领导建议说,“我在汽院读书时,常治斌老师教我们机械原理课程,听他讲过汽车前梁及半轴自动淬回火机械手传动装置,是否可请他来看看?”主管该项目的领导刘武林部长当时就同意了黄爽亮的建议,并让黄爽亮随即打电话联系我到公司生产现场了解该设备情况。通过现场查看,我心中已有把握,表示“可以试试”。我回校后组建了以金切实验室老师尹绥玉、青年教师周学良、毕业班学生刘冰与印兵、公司技术部部长刘武林和技术员姚丹为主的项目组,我任项目组长。我立即组织大家查找资料,讨论设计方案,绘制设计图纸,最终设计图纸得到公司确认,并在校办工厂完成加工制造。该改造项目是在机械式通用设备主体不变的基础上,利用冲压机曲轴伸出端作为动力输入端,增加了一套曲柄摇块与齿轮齿条组合机构的自动送料装置,与原开卷装置和卷边装置配套使用,形成了一条冲压自动线。
当时厂方为满足军需,只给了一周的安装调试时间。在调试过程中我们发现输送到冲压头下面的带料起皱,无论总么调试都不能满足要求。从理论上分析,机构的传动原理没有问题,究其原因是在设计中未考虑弹性变形和传动延迟。问题找到了,怎么解决呢?在场的人员一时谁也想不出办法,大家都很着急,时间已是周末的凌晨。当时车间的曹主任更是着急,他说,“你们先回去吧,不管怎样,明天必须给以解决,我们要完成军需产品任务。”
我们只好拖着疲倦的身体、沉重的压力,坐上尹绥玉老师的微型货车返回学校。我坐在车上沉思,突然想到,能不能在曲柄摇块与齿轮齿条组合机构的连杆上增设一个伸缩套,我立即把想法告诉尹老师。回校后,我们立即修改图纸,并进行加工,第二天送到生产现场安装调试,好啊!成功了!现场一片欢腾,大家心里别提多高兴了!散热片自动送料装置于2002年9月正式完成研制并投入生产运行。经过数万次散热片生产的检验后,通过专家现场鉴定,如图2所示。
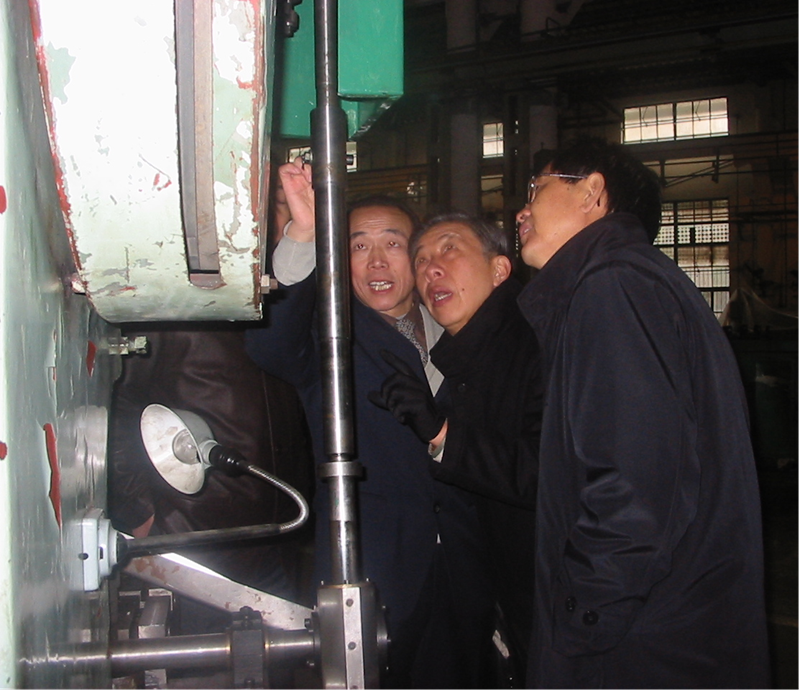
图2 鉴定专家在现场查看设备
鉴定专家认为该改造后的自动线设计合理,操作方便,各项技术性能指标均达到了设计要求。该项目为公司解决了生产难题,并一次性节约改造资金十多万元,当年被评为东风汽车公司科技进步奖。
因散热片冲压自动线的改造成功,公司领导对我们的研发能力给予肯定和认可,接着把散热管专用生产线上理料的难题交给了我们,提出由人工理料改为自动理料。在该公司领导韩力经理、技术部刘武林部长的支持下,我和尹绥玉、龙行先、周学良、刘强等项目组成员用一年多的时间,在原制管生产线主体不变的基础上,增加了一套能输送扁平薄壁轻质汽车散热管,并能将散热管按宽度方向竖直且焊缝同侧紧密排列的自动排管装置,形成了一条制管自动线。该生产线于2003年10月正式投入生产运行,每台班生产4—4.5万件,满足生产要求。该公司于2004年初将其余3条制管线予以改造,直接节约资金百余万元。经领域专家鉴定,该技术系散热器制管领域的首创,处于国内领先水平。
三、吸收改进超越洋货
汽车变速箱是汽车传动系统的重要总成,装配过程中需要将支撑传动轴的圆锥滚子轴承外圈先装配到壳体上,装配精度直接影响到变速箱的性能优劣。东风汽车变速箱公司因没有专用设备,主要靠手工进行装配。人工手锤敲击装配对轴承外圈的损伤较大且受力不均匀,装配精度低,质量得不到保证,导致客户索赔率高;同时,工人敲击装配费时费力,劳动强度较大,噪声污染严重,箱体内安装致使工人手臂经常受伤,对工人的身心健康造成一定影响,也影响了周围的环境。该公司为适应企业发展的需要,决定进行轴承压装设备研发项目招标。我们和来自重庆、苏州等五家公司参与了竞标,最终以技术优胜中标,并于2008年5月签订中标合同。接着立即成立了由汽院罗敏、龚青山、尹绥玉、张友兵、王荣志、张光国、吴岳敏,变速箱公司王勇、刘红广、刘勇、鲍伟、周金禾等参加的“中心偏差自适应轴承轴套并联压装机”项目组,我任组长。根据项目合同技术协议要求,压装机结构设计主要由压头总成、夹紧装置、升降台、移动工作台、机架、操作面板及测控系统等几部分组成;压装过程由控制系统自动控制完成,压头总成中间安装压力测量和偏差修正装置;压头可快速更换,能实现单头、双头压装。图3为东风汽车变速箱公司设备工程师在现场查验压装机设备。
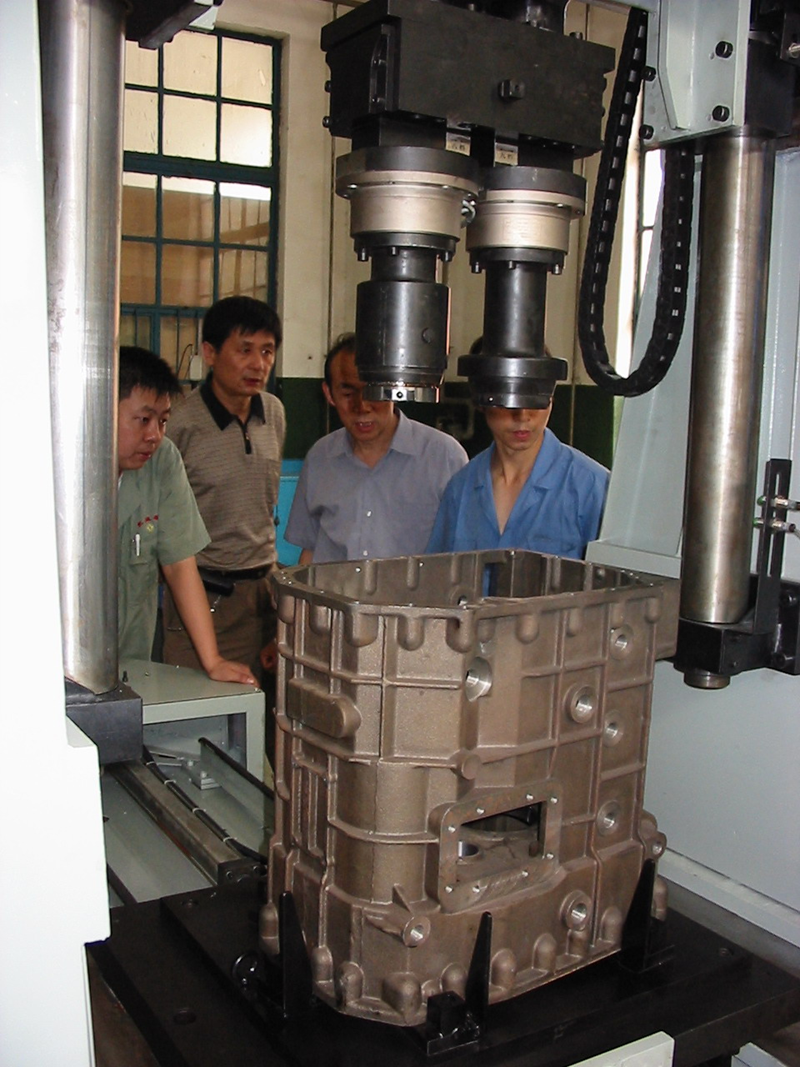
图3 公司设备工程师在现场查验压装机设备
压装过程中多压头中心与工件多孔中心之间的偏差能自动对中是项目的关键技术,最初选购了韩国生产的Center-Master偏差修正装置,安装在气缸与压头之间。在生产现场试压时发现,两中心偏差有时不能得到修正,导致两压头将两轴承外圈压入轴承孔中后压头卡在轴承孔中,退回时将箱体带起来,无法退出。经多次试验确认,该韩国生产的偏差修正装置不能满足要求。我们只好把压装机搬回学校改进。查阅了很多文献资料都未见相关报道,最后把韩国Center-Master偏差修正装置拆开,终于找到了问题问题所在,原来是弹性加滑动,压死后无法动。几天冥思苦想,突然想到若改成滚动情况怎样呢?想法有了,立即绘制图纸、加工、安装调试,最终满足了变速箱轴承轴套压装要求。利用滚动摩擦阻力小的原理,研制的中心偏差自动修正对中装置,解决了压装过程中压头中心与轴承孔中心之间的偏差能自动修正对中的技术难题,实现了压装技术上的突破,获得3项国家专利。该项目整机性价比高,部分性能指标优于同类进口产品,超越洋货。
四、产学研路越走越宽
时光飞逝,转眼四十余载。在学校领导和各级部门领导的关心及支持下,通过校企产学研合作,我和同事们一起承担完成的《机械手传动装置》、《轴承轴套并联压装机》、《多功能大型展示车》、《弯扭疲劳试验台》、《冲压自动线改造》、《自动排管机》、《降噪设备》等应用型技术研究成果直接转化并推广应用于汽车制造生产中,取得了数千万元的经济效益和良好的社会效益,同时也获得了多项湖北省重大科技成果、国家专利,发表相关论文数十篇,几十名学生通过参与相关课题完成毕业设计获得了锻炼。
我们承担的绝大部分课题大都以机、电、汽车制造为基本主攻方向,开展工装设备、检测、汽车制造及计算机应用等方面的研究与开发,以企业的发展需要确定研究课题,并由企业提出明确实用的技术要求,在研发过程中不断与企业沟通交流,进行改进,以保证研究成果最终能投入使用。这样的科研,教师有收获,资金有保障,学校有成果,企业有效益。不仅提高了我们的理论水平与研究能力,同时解决了企业的实际问题,使学校为东风汽车公司的科技进步做出了应有的贡献。一个机械工程项目需要设计、加工、调试,安装、组织、管理等多方面的技术,缺少任何一个环节都可能严重影响课题的最终质量,甚至会导致整个项目的失败。因此,我们所承担的项目需要企业委托单位的密切配合,课题组由厂校双方的人员组成,优势互补,学校无法解决的加工、调试等问题,正好是企业的强项。经过承担校企合作研究课题,我们得到了锻炼,提高了承担科研项目的综合能力,课题组部分老师也已成长为相关方面的专家。
经过多年的实践,我们认为产学研校企结合,既能提高教师的科研能力又促进了课程建设、专业建设与团队建设;教师承担实际课题,结合典型案例讲课会更加生动,便于学生理解;同时结合工程实际进行毕业设计,能充分调动学生的主观能动性,有利于培养学生的工程意识和创新能力。
我们的科研在校企产学研合作方面取得了一定的成效,我们也越来越认识到科研与企业结合的重要性,只有坚持校企产学研合作,路才会越走越宽。我们的教科研工作必须走产学研结合之路,根据汽车行业发展方向确定团队建设与人才培养目标,以企业发展所需确定科研课题和科研团队研究方向,以解决企业急需问题为抓手,把团队建设、人才培养和企业生产需要三者相互结合、相互促进、相互依存,实现优势互补、共赢发展。学校的办学指导思想越来越明确,努力方向和奋斗目标已确定。学校积极引导、鼓励教师不忘初心、牢记使命,为振兴祖国汽车工业,为祖国建设和发展输送更多德才兼备的建设人才,发扬百折不挠的革命精神,坚持一丝不苟的科学作风,把科研论文写在工厂里,写在车间里,把科技成果运用到实践中,相信学校建成国内一流应用研究型大学的目标一定能够实现。
作者简介
常治斌,1950年出生于郧县,教授。1976年毕业于湖北建筑工业学院(现武汉理工大学)机械系建材机械专业并留校任教。1982年12月调入永利www官方网址工作,历任机械设计教研室副主任、机械工程系(学院)副主任、主任、党总支书记、校学术委员会副主任、校教学督导组组长、湖北省教育厅教学巡视组组长等职。
他从事高等教育40余年,忠诚党的教育事业,敬业爱岗,严谨治学,教书育人,致力于汽车制造装备技术方面的教学与研究。主讲机械原理、机械设计、机械创新设计等课程,并担任研究生导师。教学中重视教学改革与创新,将科技创新成果融入教学内容,把课堂教学与课外科技活动紧密结合,形成了独特有效的教学风格,提高了学生的创新意识与创新能力,其《开展课外科技实践活动培养学生创新意识与创新能力研究》教学研究项目获湖北省教学成果一等奖。
他任机械工程系主任工作期间,注重团队建设,带领全系教职工以奋发有为的进取精神、与时俱进的创新观念、扎实工作的务实态度,在提高人才培养质量和学科专业建设上狠下功夫,先后被湖北省授予“省级重点学科”、“省级品牌专业”、“省级精品课程”、“省级实验示范中心”、“省级教学团队”称号及“机械工程硕士学位授权团队建设点”。
他主持完成省级及以上教科研项目十余项,其中获湖北省教学成果奖3项、湖北省重大科技成果6项,国家专利10项,发表论文40余篇,主编和参编教材及手册6部,指导学生科技竞赛和毕业设计获省级奖20余项。主持完成的科研项目大多为企业技术开发实际工程项目,其《中心偏差自适应轴承轴套并联压装机》、《自动排管机》、《多功能展示车》等研究成果直接转化并推广应用于汽车制造生产中,已取得了数千万元的经济效益和良好的社会效益。
常治斌同志在提高人才培养质量和学科专业建设及为汽车行业和地方经济发展付出了智慧与汗水,作出了突出贡献,诠释了汽院人的忠诚与担当。
常治斌同志退休后,仍不忘初心,继续关心学校和地方经济发展与科技进步,积极建言献策出力。被聘为永利www官方网址教学督导组副组长、十堰市机械工程学会副理事长、市工业经济咨询委员会委员、市老科技工作者协会理事、湖北省机械工程学会理事。“莫道桑榆晚,为霞尚满天”,再谱人生新篇章。